6/25/25
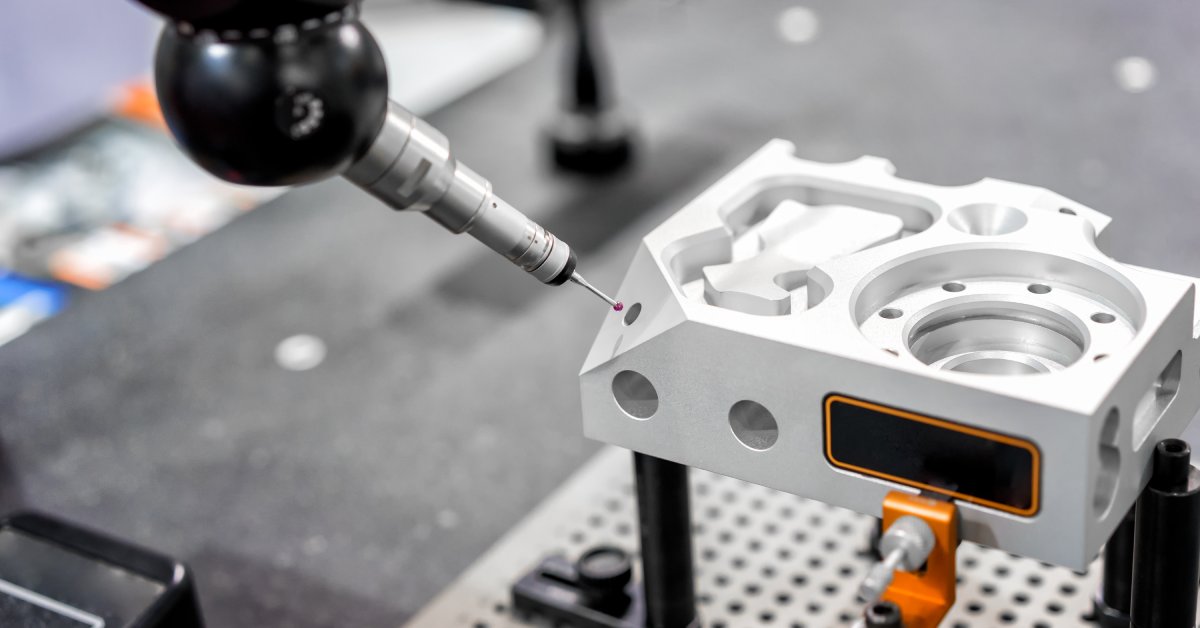
The History and Evolution of CMM Technology
Coordinate-measuring machines (CMMs) have revolutionized the way manufacturers ensure precision and quality in production. By enabling accurate, automated measurements of complex components, CMM technology has become a cornerstone of modern quality-control processes.
The history and evolution of CMM technology reflect humanity’s continuous drive to achieve perfection in measurement and manufacturing processes. We’ll explore how CMMs have transformed manufacturing, from early manual machines to state-of-the-art, software-driven solutions, and what the future holds for this critical technology.
The Origins of Measurement in Manufacturing
Accurate measurement has always been a critical aspect of manufacturing. Long before the advent of modern technology, ancient civilizations devised tools to ensure consistency. Egyptian stone masons and Roman architects laid the foundation for today’s precise techniques centuries ago by using calibrated ropes and developing early measurement standards, respectively.
Fast forward to the Industrial Revolution, when mass production called for a more systematic approach to measurement. Traditional tools like calipers and micrometers enabled greater accuracy but required manual effort and expertise. While effective for their time, these tools were limited in precision and unsuitable for measuring complex geometries. This demand for higher accuracy in increasingly complex industrial processes set the stage for the development of coordinate measuring systems.
The Birth of CMM Technology
CMM technology emerged in the mid-20th century as a game-changer for industrial measurement. Early CMMs were simple three-axis measurement tools designed to assess the spatial coordinates of objects. They provided manufacturers with an unprecedented ability to measure parts accurately and consistently.
Ferranti manufactured the very first CMM machine. This British company was the launching point for other developed countries, like the USA and Germany, to hop on the CMM machine trend. The first public appearance of a CMM machine appeared at the 1959 International Machine Tool Exhibition in Paris.
These machines revolutionized quality control in the aerospace and automotive industries. The basic concept was this: move a probe along three Cartesian coordinates (X, Y, Z) to capture a part’s dimensions. Early CMMs were primarily manual, requiring technicians to carefully manipulate the machine and record data manually.
While groundbreaking, these rudimentary machines relied heavily on operator skill and offered limited speed. However, their impact was undeniable, setting the stage for a wave of innovation.
The Evolution of CMM Design
Early Manual CMMs
The earliest CMM designs focused on simplicity. These devices were manually operated, requiring operators to guide the probe and record measurements. While they offered enhanced accuracy compared to traditional measurement tools, they were labor-intensive and prone to human error.
These early models mainly found their place in industries where precision was paramount. However, their long setup time and limited features underscored the need for automation in coordinate measuring systems.
The Shift to CNC CMMs
The introduction of computer numerical control (CNC) CMMs in the 1970s was a significant breakthrough. These machines integrated computer control, automating the measurement process and standardizing operations. CNC CMMs allowed technicians to program inspection routines, ensuring consistent results across multiple batches of parts.
With CNC technology, manufacturers saw drastic reductions in inspection times and errors. This innovation also made it possible to measure increasingly complex surface geometries, aligning well with the growing intricacies of modern manufacturing processes.
Advancements in Probing Technology
Another major leap in CMM evolution has been advancements in probing technology. The earliest CMMs relied on contact probes, which required physical touchpoints to capture measurements. Over time, optical and laser-based systems were introduced, allowing machines to measure without physical contact.
Contactless systems ushered in new opportunities, particularly in industries where delicate materials or rapid scanning required noninvasive techniques. Meanwhile, advancements in sensor technologies ensured that even contact-based probes became faster and more accurate.
The Role of Software in CMM Technology
The hardware advancements in CMM technology would not have been as impactful without parallel improvements in software. Modern CMM software has evolved to process large data sets, generate 3D models, and provide actionable insights. These systems ensure seamless integration with other digital tools, enhancing the capabilities of the hardware itself.
Many software systems today come with features like error analysis, automated calibration, and real-time reporting dashboards. This makes CMM technology an essential component of custom measurement solutions tailored to specific production needs. The alignment between hardware precision and software flexibility is at the heart of modern CMM success.
Modern CMMs: Features and Capabilities
Today’s CMMs are engineering marvels, equipped with advanced capabilities that once seemed futuristic. Key features include the following:
- Multi-sensor capabilities: Modern machines can integrate tactile, optical, and laser systems for versatile inspections.
- Automation compatibility: Many CMMs can now be paired with robotic arms or placed on production lines for fully automated inspections.
- Environment adaptability: Active temperature compensation ensures that measurements remain accurate under varying environmental conditions.
- High-speed scanning: Advanced probes enable rapid data collection without sacrificing precision.
These features allow CMMs to play vital roles in industries such as aerospace, automotive, medical devices, and beyond.
The Impact of CMM Technology on Manufacturing
The widespread adoption of CMM technology has redefined manufacturing in several ways:
- Improved quality control: By delivering highly accurate measurements, CMMs have eliminated guesswork and reduced product defects.
- Enhanced productivity: The automation and reliability provided by CMMs have significantly reduced the time spent on inspections.
- Cost savings: Consistency in measurements translates to less material waste, lower rework costs, and improved overall efficiency.
CMMs also foster innovation. With precise measurements enabling complex designs, manufacturers can explore new materials, forms, and functions with confidence.
Challenges and Limitations of CMM Technology
Despite its capabilities, CMM technology is not without challenges. High acquisition costs can deter smaller businesses, and the need for skilled operators to program and maintain these machines is crucial.
Additionally, while modern machines are highly efficient, some industries present unique challenges, such as inspecting ultra-dense materials or handling large-scale components. However, ongoing advancements are addressing these issues.
The Future of CMM Technology
The future of CMM technology is tied to developments in artificial intelligence, machine learning, and the Internet of Things (IoT). Smart CMMs are expected to leverage these technologies for self-calibration, predictive maintenance, and real-time optimization. Additionally, cloud-based systems may allow manufacturers to centralize data, making measurements accessible across multiple locations.
As these advancements unfold, the history and evolution of CMM technology will continue to influence how industries operate. One thing is clear—CMMs are essential to achieving precision in a world that demands nothing less.
Choosing the right partner for your CMM stylus needs is crucial to achieving precision and reliability in your measurements. At itpstyli, we offer an extensive range of high-quality styli that meet the varying demands of different CMM applications.
Don’t see a stylus fit for your industry? We can collaborate with you to develop custom solutions. With a deep understanding of metrology and a commitment to delivering superior performance, itpstyli is the trusted choice for those seeking to maximize accuracy and efficiency in their inspection processes.